
STATES OF MATTER
Wool fibers and non-traditional methods of chemically extracted keratin
FABRICADEMY 2021 / 2022
The food industry and mass production have been producing much wool waste for a long time. The wool goes beyond the boundaries of textiles. The project investigates the chemical properties of wool fibers by extracting keratin and implementing it in the fabrication of new biomaterials. It aims to define a new value of wool as a material using current technologies and design as a tool. It analyzes wool in all states of matter using green chemicals, biomaterials and additive manufacturing.
The material research focuses on keratin extraction, DIY fabrication and the usage of sustainable chemicals in the extraction process. The extraction is adapted to DIY laboratory tools that can be easily made and used to produce (im)pure keratin as an open-source material. The extracted keratin is used as liquid or powder to refine the properties of the produced biofilms or composites in combination with other additives. Their combination is investigated in terms of possible applications for 3D printing technology. Its waterproof and fire-retardant properties are reflected in coating agents for textiles. All possible outcomes of the project will be found in a material library which represents a challenge for the post-processing of wool waste.
The States of Matter project has been awarded the Young Scientist Award 2022.
STEPS
-
I. Wool pre-treatment
We use acetone or ethanol to clean all dirty parts of wool fleece and remove first layers of wool fiber (cortex & cuticle) and lanolin. Then we are able to more easily open the fiber bonds.
-
II. Chemical dissolution
The wool fiber will disappear in chemical solution with urea and NaOH. That means its additional layers of wool fiber will be destroyed. You will achieve a liquid yellow/brown solution which you will need to clean. Keratin is now still mixed with the rest of the chemicals.
-
III. Filtration & Centrifugation
Filter and purify the extracted solution. Centrifugation serves as a tool to separate chemical molecules from molecules of wool protein. The DIY centrifuge is made of an electric drill and 3D printed parts.
-
IV. Biuret test
Protein presence test with home-made Rochelle crystals.
-
V. Dialysis
Instead of cellulosic dialysis tubes we will use a cow stomach to filtrate the extracted solution from the rest of the chemicals.
-
VI. Freeze-drying
DIY Freeze dryer in YOUR LAB SOON!
CHEMICAL EXTRACTION
The project aims to find the most suitable and efficient way to chemically extract keratin from wool fibers. Subsequent processing into powder or liquid and its incorporation into the production of materials and additives. At the same time, research emphasizes the importance of the textile industry processing wool. Also, other textiles that are undergoing harmful chemical treatment or production. The project is experimenting with waste wool as a leftover of mass food production.
The main plan at the beginning of the research was to use Ionic Liquids (ILs) during the extraction process. ILs are salts composed of an organic cation with different organic and inorganic anions with a melting point below 100 ° C. They are considered new green solvents as a new sustainable way to extract keratin from wool fibers. This method of extraction proved to be unavailable in our conditions. ILs are not readily available due to their high cost
BIOPLASTICS
Keratin has been originally used to produce biofilms that differ from bioplastics by living composition. Biofilms are used as advanced biomaterials because they can produce the growth of organism cells. However this material research does not produce pure keratin that could be used to form biofilms. It can be used to produce bioplastics.
Bioplastics try to replace the original plastic packaging or foils, for example for food packaging due to their biodegradability. Not all have the same sustainable properties. They consist of a polymer, usually of food origin, and a plasticizer (glycerol) which regulates the flexibility of the material. Various additives are added to the initial recipe as needed to change the color, quality or texture.
In most of the bioplastics tested in this study, keratin is blended with another polymer to achieve different final material qualities. We can create a material library of various examples in which forms of biomaterial can be applied and researched.
3D PRINTING
The 3D extruded material and its parameters with respect to the emerging geometries has been investigated. Keratin powder acts as an impurity in the material formation process in these experiments. The aim is to test its ability to form bonds with other polymers and to find a suitable form that can be used in the design industry.
Following bioplastic experiments, keratin was found to form bonds with materials other than the protein itself. Among the first attempts to create a mass for 3D printing was a combination with sodium alginate, tapioca, corn starch and guar gum, whether in powder or liquid form.
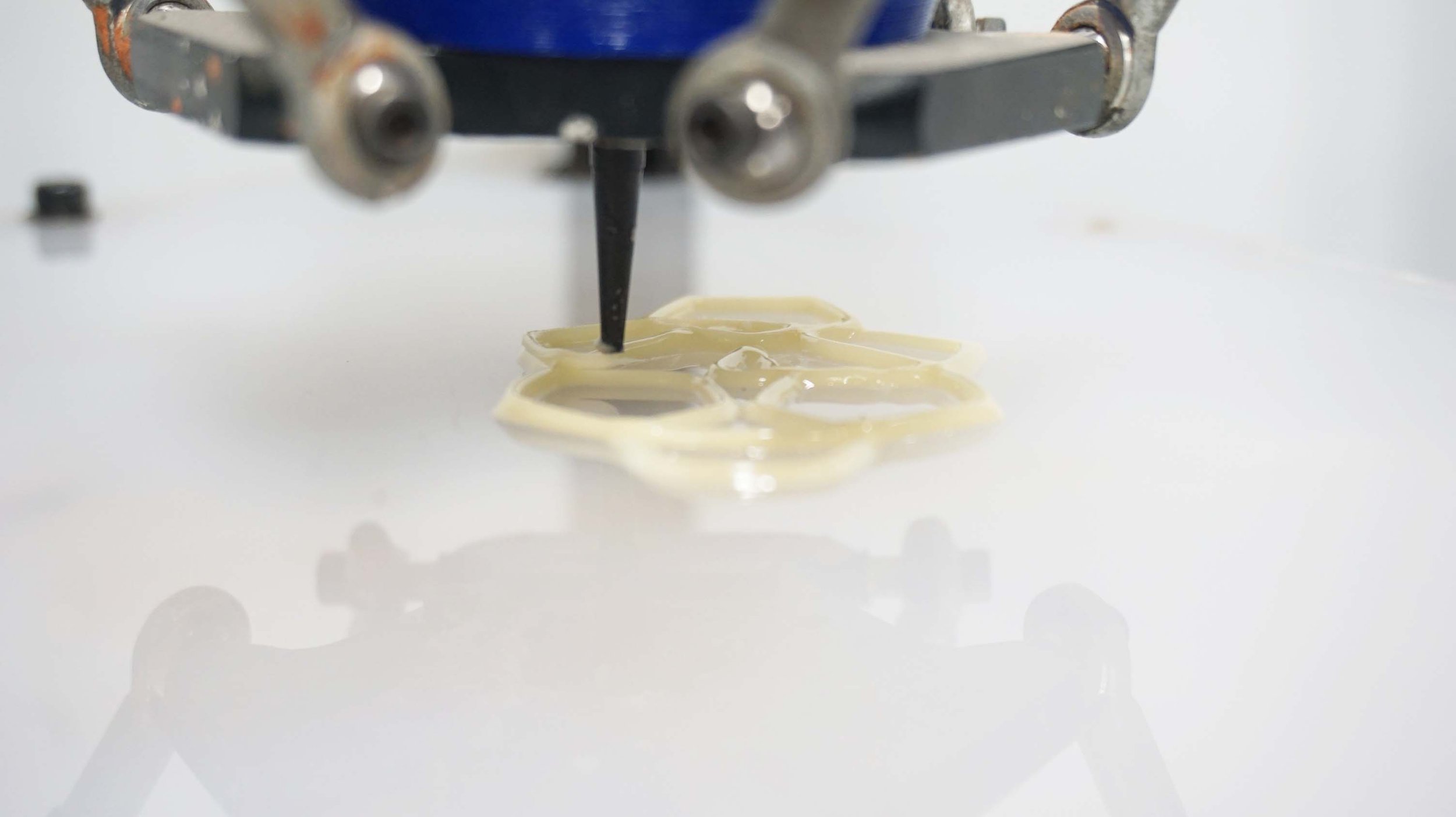
ELECTRO-SPINNING
DIY electro-spinning machine is not a safe device but it has a multi-material application. The creation of nano or microfibers is used. It consists of a syringe filled with liquid material when the syringe needle is connected to a high-voltage generator. The content of the syringe is spun or sprayed on a metal collector that is connected to a high-voltage generator too. This creates an electrical voltage between the collector (negative), the needle (positive) and the material. The collected material impinges on the metal collector and thus creates a thin layer of fibers. Then it is removed together with the aluminum foil. Any PVC, PLA or biomaterial in liquid form can be used as the material. An important factor during the use of the DIY Electro-spinning machine is the high voltage generator which is life-threatening.
TEXTILE COATING
Chemicals and several repetitive processes are currently used to impregnate textiles. None of them use waste or more sustainable materials. The ability to repel water, and protect from fire or wind makes textiles wanted in the fashion market. Finishing is the last step in adjusting fabrics or yarns during the manufacturing process. There are currently three types of textile finishing - coatings, laminates and finishes. The visible layer which rather resembles plastic is called coating and is usually used in sportswear. Where two or three coats are applied on both sides to protect the fabric from several natural conditions at once. Laminates on the other hand can only be found as one layer. It is usually applied on the inside of the dress and is highly breathable but not very affordable. Laminates and finishes have a common transparent texture but finishes have protective properties that can be used in protective clothing against chemicals.
The uniqueness of keratin lies in its hidden chemical properties such as water resistance and slow burning. We can implement its uniqueness in textile finishing. We will create a new layer thanks to spraying keratin on the surfaces of fabrics. Then we can improve their resistance to water and fire. Finishing with keratin spray, subsequent pressure and rinsing saves energy and does not use excessive amounts of chemicals. Compared to other methods excessive water consumption is not required and more efficient results of the final textiles are achieved.
DIY TOOLS
A centrifuge is a laboratory device that is used for the separation of fluids, gas or liquid, based on density. Separation is achieved by spinning a vessel containing material at high speed; the centrifugal force pushes heavier materials to the outside of the vessel.
Last but not least, the material research is based on local conditions and materials more than could have been expected at the beginning. Other domestic materials or chemicals were used in addition to the use of local wool. The same applies to the available technology. It provided us with unique solutions together with creativity and offered new solutions in difficult situations. Compared to protein extractions from plants, animal fibers are much more demanding. It goes through a more complicated and strenuous process. However, despite these time or other technical hurdles, materials research has found its purpose and its first successful prototypes such as bioplastic samples or 3D printed prototypes.
The concept of this three months materials research is based on my architectural background but with great interest in the textile industry. Which clearly marks the whole process of prototyping and experimentation. It meets with positive feedback from fields such as chemistry, biology, or from specialists who have worked on the handcraft techniques during their lifetime. Whether it is an advantage or disadvantage of knowing the chemical process is more important than traditional wool work it will remain as an unanswered question. At the end of my research, I worked with wool such as weaving or spinning techniques which gave me a completely different material knowledge. We cannot exactly define the boundary where material innovation meets design. The research clearly reflects artistic conceptual thinking which makes it unique with its curious path.
Watch the video documentation of the research project.
Read the thesis here.
Fabricademy documentation can be found here.
Green Product Award´s Nomination website.
Technical Textiles Magazine article read here.